All wind turbines have a notional design wind speed. If the wind is at this speed or above it, the turbine rotor produces the same net power output. The rotor blades are pitched so as not to gather more mechanical power than can be converted. The situation is more complicated if the wind speed is below rated speed. Then the optimal rotor speed is proportional to the wind speed and the torque exerted on the rotor by the power transmission system must be just right to achieve the optimum energy extraction from the wind. This requires that the power transmission system can operate at part load.
The WindTP power transmission can operate very effectively at part load. In the standard design, each stage of the primary compressor, secondary compressor and expander comprises 12 different cylinders in that stage of the displacer part and a corresponding 12 cylinders in the converter part. Thus, in any one cycle, that stage can operate 0/2/3/4/6/8/9/12 cylinders and it can retain perfect balance. Because there are plenum chambers between successive stages of the compressor, different stages can operate at different fractional loads at the same time. The first stage might alternate between having 2 cylinders active or 3 cylinders active per cycle. Other stages would then do the same and the net effect here would be that a part load operation of (5/24) would be achieved. Thus there are very many different combinations of possible loads that can be sustained – without compromising efficiency substantially.
The same principle applies perfectly well to the secondary compressor and to the expander.
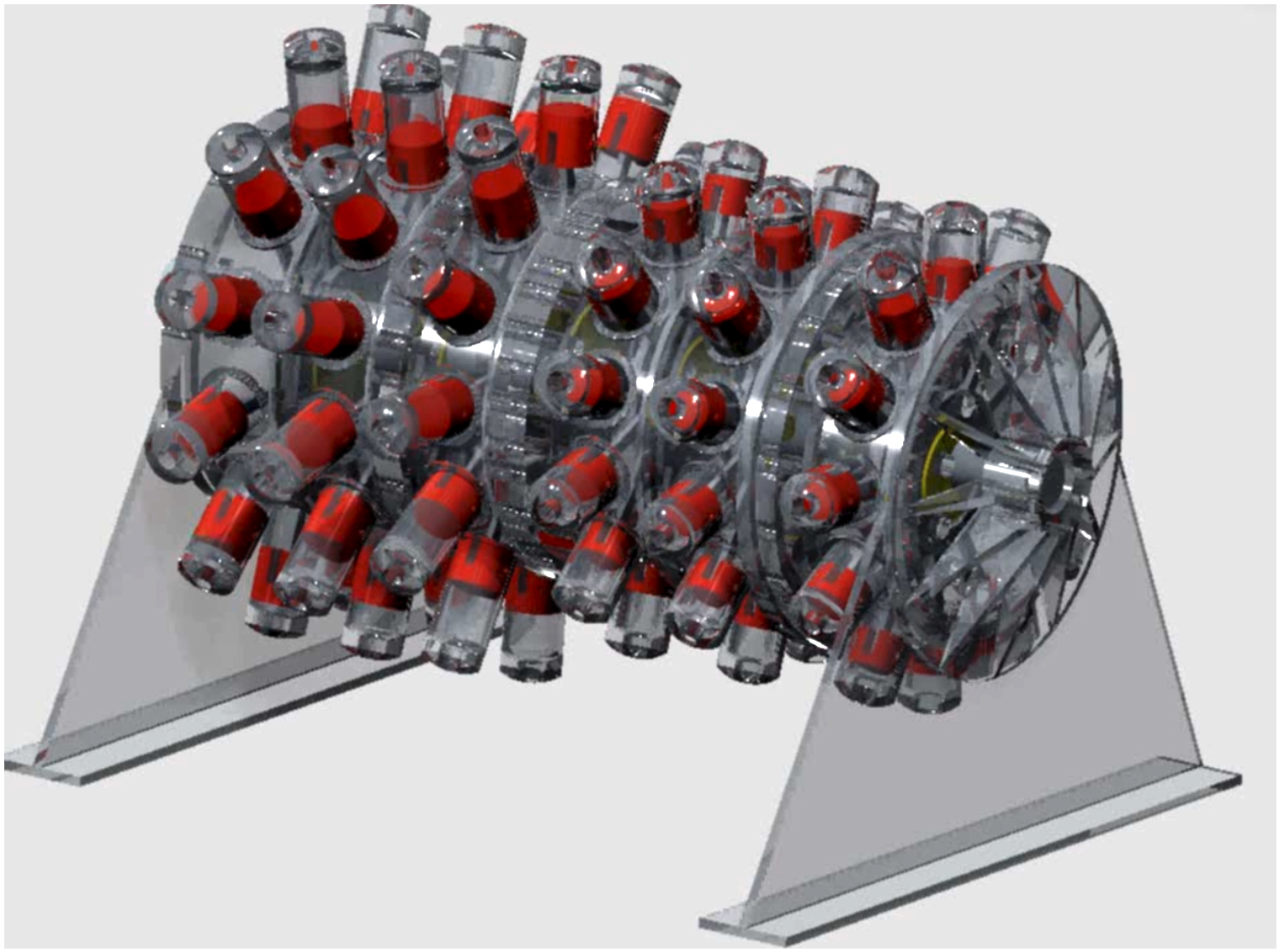